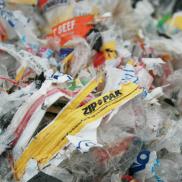
Since its introduction in 1862, plastic has been an integral component of our daily lives, from our alarm clocks to our trendy smart phones, chairs, tables, refrigerators, grocery bags; the list goes on! As a result of our head-over-heels dependence on plastic, production and consumption is rapidly increasing and every year we make enough plastic film to shrink-wrap the state of Texas.
After plastic reaches the end of its useful life cycle, it is disposed of in four different ways:
1. Recycling: According to the Clean Air Council, 13.3% of plastic was recycled in 2008, but recycling is proving to be inefficient and expensive because of the limited types of plastic that can be recycled and the high cost associated with the recycling process. Recycling one metric ton of plastic bags costs $4,000. The recycled product can be sold for $32. This low profit margin results in less than 1% of plastic bags being recycled each year.
2. Landfills: Plastic waste can take as much as 1,000 years to decompose and can potentially leak harmful pollutants into soil and streams. Hence, landfill dumping creates considerable environmental damage. Not to mention costs associated with landfill dumping can be up to $200 per ton.
3. Incineration: Waste is put through a high temperature combustion process, where the plastic waste is burned and produces hazardous atmospheric emissions and toxic ash. Incineration has proven to be extremely harmful to the environment and therefore this process has rapidly declined in popularity in the US.
4. Worldwide Dumping: Lastly, not all plastic is lucky enough to get recycled, buried in a landfill, or incinerated. Today, the most common way to dispose of plastic waste is by abandoning it in different areas around the globe. This causes significant environmental degradation. The oceans in particular suffer from extreme pollution and are called “world’s largest waste dump”. A floating mass of approximately 100 million tons of mostly plastic waste has given Pacific Ocean the name of “Great Pacific Garbage Patch,”.
Are we are running out of options?
Maybe not. Research and development has given birth to a technology that facilitates the management of plastic waste by transforming plastic waste back into its original form ? crude oil. Yes, you are reading correctly ? crude oil. There are companies working towards converting the low value plastic waste into a high value crude oil. The arrival of this new technology could potentially reduce America’s dependance on foreign oil sources and reduce our landfill waste.
Since plastic is a derivative of petroleum, plastic has a high level of stored energy content that is comparative with gasoline and about 51% higher than the energy content of coal. This residual energy goes to waste when plastic is discarded into streams or dumped into landfills. This new conversion process capitalizes on this discrepancy and recaptures the valuable energy stored in plastic.
While the waste-to-energy process is nothing new, it’s not widespread in the United States. There are companies in America, such as Envion, John Bordynuik, Inc. (JBI), Dow Chemical Company and Agilyx, working towards fulfilling the tasks of commercially converting tons of plastic waste into oil. Agilyx, a start-up in Portland, Oregon has already turned approximately 1 million pounds of disposed plastic into more than 120,000 gallons of crude oil that has since been sold to clients. Production of converted oil costs about $50 – $60 per barrel and according to NYMEX, this is still less than the current price America pays to import crude oil which ranges from $70 ? $100 per barrel. Plus, don’t forget we are cleaning the waste from the environment and making it even more useful by producing a valuable commodity. In addition, a Japanese inventor has created a machine for home use that can turn plastic waste into fuel.
This technology uses plastics as a feedstock and converts difficult-to-recycle waste plastics into separated, refined fuels. This process includes easy installation and operation, high efficiency (about 80-90% feedstock gets converted), and high value output in the form of crude oil that can be further refined to produce gasoline. Most importantly, this conversion process produces no secondary pollution as the residue is transformed into emulsified heavy oil while vent gas is recycled within the unit for electricity generation.
Envion states:
“This innovative approach produces oil and power safely, efficiently, and economically through an environmentally sensitive process that produces a net gain in energy recaptured.”
Although production depends on the type of plastic used as a feedstock, each ton of waste produces approximately 3 to 5 barrels of product.
The success of this new technology hinges on the technology working on a large scale and being efficient enough to generate a win-win situation for the environment, producers and the consumers. The most crucial part is making the conversion from plastic to oil an efficient process. This new invention could change the way plastic waste has been treated for centuries and also protect the environment from further degradation.